- Commercial
- Industrial
Reaching New Heights in Self-Performance
October 20, 2020

Brasfield & Gorrie is known for our concrete expertise. We often complete concrete work using our own forces, which gives us superior control over schedule, cost, quality, and safety. And we continue to push forward, learning and growing expertise even in areas where we have a half-century of experience.
That’s exactly what we did in partnership with TK Elevator as we used slip-form construction to build the company’s elevator test tower in Atlanta. Slip-form construction uses a moving formwork system from which crews continually place concrete. Slip-form is common in Europe—in fact, TK previously used it to build a tower in Rottweil, Germany—but the technique isn’t common in America.
The project includes an innovation and qualification center (IQC) and corporate headquarters, and the centerpiece of the IQC is the elevator test tower. This more than 400-foot-tall freestanding tower had to meet specific quality, budget, and schedule criteria. Slip-form construction allowed the team to meet the client’s quality expectations for the test tower’s 398.5-foot concrete shaft.
Because Brasfield & Gorrie doesn’t perform slip-form construction regularly, we sought leadership from General Superintendent Lynn Walker and guidance from international slip-form experts Gleitbau-Salzburg. A self-perform specialist, Walker contributed previous experience with slip-form construction from past jobs.
Precise Process
TK Elevator required uniform wall thickness and extensive coordination for the test tower’s many embedded elements. The concrete slip-form system was the only way to produce the test shaft specifications safely, on schedule, and within the required tolerances. The process enabled our team to complete the work in 54 days of continuous slip-form operation, plus three days for crane jumps.
Walker said slip-form requires a team that’s dedicated to accuracy. The project used lasers to align the slip-form system, and the team checked eight times a day to ensure that the form remained plumb as the tower rose.
Going Up
The project’s slip-form system used several platforms from which workers continuously placed concrete, installed rebar, placed more than 3,000 embeds and 190 openings, installed conduit, and finished the concrete. These activities required a 24/7 operation with three crews that rotated on 12-hour swing shifts.
The platforms moved as a unit. The slip-form system is extremely safe as it is completely enclosed on the main working deck, first hanging deck, and second hanging deck. The system moved constantly, rising approximately 1 inch every 15 to 20 minutes.
No Mix-Ups
Concrete mix design was essential to the operation’s success. The slip-form cannot rise until the concrete inside of the form has set. Having the correct mix allowed the workers on the system to control the speed. We had to perform several test placements to monitor cure times before the start of the operation so we could set baselines for set times of each mix. By the end of the operation, our team had nine mixes with set times that varied from 5 to 18 hours. The mixes with higher set times were used for floors with many embeds and when we needed to stop for a crane tie-in. It was also important to keep the water-to-cement ratio above .40 to create a workable surface for the finishers to refine.
New Heights
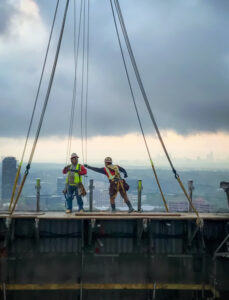
The test tower reached its full height in mid-March, and the IQC is on track for completion in the third quarter of 2021.
“We were happy that the job exceeded its tolerance qualifications,” Walker said. “We were able to beat the schedule substantially. Most importantly of all, we didn’t even have one recordable safety incident all the way up and all the way down.”
Walker said slip-form is ideal for elevator cores in high-rise buildings, and we look forward to additional opportunities to use this innovative self-performance technique.
Related